Composite Prüfdienstleistungen
Prüflabor akkreditiert nach DIN EN ISO/IEC 17025:2018
Überblick
Grasse Zur Composite Testing bietet an seinem Standort in Berlin Materialprüfungen in einem weiten Bereich nach allen gängigen Prüfverfahren für faserverstärkte Kunststoffe an. Die Prüfdienstleistungen werden in dem nach DIN EN ISO 17025:2018 akkreditierten Materialprüflabor durchgeführt und umfassen das gesamte Spektrum der Materialprüfung. Die Auftraggeber aus der Luft- und Raumfahrt, dem Automobilbau oder der Chemieindustrie kommen in der Regel aus dem Bereich Entwicklung (Simulation bzw. Neuentwicklung) oder Produktion (Wareneingang bzw. produktionsbegleitende Qualitätssicherung). Der Fokus der Prüfdienstleistungen liegt gleichermaßen auf der quasi-statischen (und zum Teil dehnratenabhängigen) Materialprüfung, der zyklischen Materialprüfung (Ermüdungsversuche) und der Thermoanalyse (DSC, DMA, etc.). Die Prüfungen erfolgen nach allen gängigen Prüfverfahren entsprechend DIN EN ISO bzw. ASTM. Zusätzlich verfügen die Mitarbeiter des Prüflabors über ein umfangreiches Know-how von Normen aus vielen anderen technischen Anwendungsbereichen.
Zur Bestimmung der quasi-statischen Materialeigenschaften werden Materialprüfungen an elektromechanischen Prüfmaschinen im Kraftbereich von 1…100 kN durchgeführt. Die zyklischen Materialprüfungen erfolgen an servohydraulischen Prüfmaschinen im Kraftbereich von 1…50 kN. Die Probekörperklemmung wird über hydraulische Keilspannsysteme für Flach- und Rundspannung (0…25 mm) realisiert. Auf den servohydraulischen Prüfmaschinen können ein- und mehrstufige Ermüdungsversuche zur Ermittlung von Wöhlerlinien und Haigh-Diagrammen durchgeführt werden. Eine Vielzahl von Prüfvorrichtungen steht für die unterschiedlichsten Prüfanforderungen zur Verfügung.
Portfolio
Das Leistungsangebot umfasst von der Herstellung von Laminaten im VARI-Prozess über eine CNC-gesteuerte Probekörperfertigung bis zur Durchführung der Materialprüfung das komplette Feld der Materialprüfung. Weitere Prüfungen wie z.B. Bestimmung des Aushärtegrads oder des Faservolumengehalts erfolgen optional. Die Konditionierung der Probekörper sowie Prüfungen bei verschiedenen Temperaturen runden das Portfolio ab. Spezielle Prüfanforderungen wie Lagerung in Kraftstoffen oder fraktographische Untersuchungen an Schliffbildern werden flexibel und schnell umgesetzt. Die Herstellung und Prüfung von Reinharz-Materialien aus EP- oder VE-Harzsystemen ist ebenso problemlos realisierbar wie Fallprüfungen zur Bewertung des Splitterschutzes. Für die Prüfungen werden ausschließlich kalibrierte Meßmittel verwendet. Entsprechend den Anforderungen der Luft- und Raumfahrt kommen zur Bestimmung der Moduln und der Poissonzahlen nur Dehnungsmessstreifen zum Einsatz, um eine präzise Messung der Werkstoffverformung zu gewährleisten.
-
Auftragsbestätigung
Nach Angeboterstellung und Beauftragung erhält der Auftraggeber von uns eine Auftragsbestätigung.
-
Materialeingang
Der Materialeingang wird entsprechend unserer Akkreditierung nach ISO 17025 dokumentiert.
-
Zeitplanung
Am Tag des Materialeingangs erhält der Auftraggeber eine detaillierte Zeitplanung für den Prüfauftrag.
-
Probekörperherstellung
Die Probekörperherstellung erfolgt mit CNC-gesteuerten Maschinen und umfasst ggf. auch die Applikation von DMS.
-
Vermessung
Die fertig hergestellten Probekörper werden mit kalibrierten Meßmitteln vermessen.
-
Prüfung
Die Materialprüfung erfolgt an kalibrierten Universalprüfmaschinen bzw. Analysegeräten.
-
Erstellung des Prüfberichts
Die aussagekräftigen Prüfberichte enthalten in übersichtlicher Darstellung alle Prüfergebnisse sowie detaillierte Photos.
-
Versand der geprüften Probekörper
Je nach Beauftragung erfolgt der Versand der geprüften Probekörpern rückverfolgbar und sicher verpackt.
-
Ergebnisübersicht
Zum Abschluß des Prüfprojektes erhält der Auftraggeber eine übersichtliche Ergebnisdarstellung.
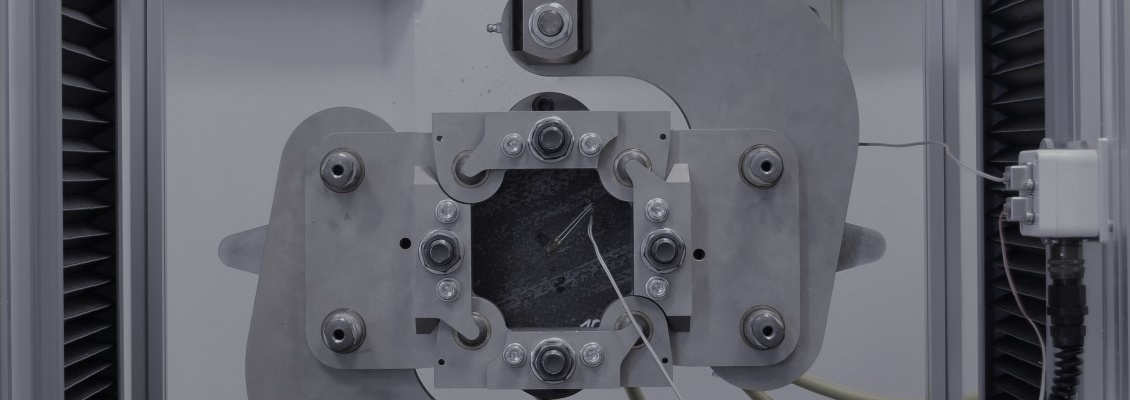
Composite Zugprüfungen
Im Zugversuch werden die mechanischen Werkstoffkennwerte unter quasi-statischer Zugbelastung ermittelt. Der Zugversuch gehört zu den am häufigsten durchgeführten Prüfverfahren und wird auch für Composite-Werkstoffe wie kohlenstoff- oder glasfaserverstärkte Kunststoffe angewendet. Grundsätzlich wird zwischen isotropen, anisotropen und orthotropen Werkstoffen unterschieden. Bei anisotropen Werkstoffen ergibt sich in Faserlängsrichtung (0°-Faserorientierung) eine Faserbruchbelastung (FB) und in Faserquerrichtung (90°-Faserorientierung) eine Zwischenfaserbruchbelastung (ZFB).
Um qualitativ hochwertige Versuchsergebnisse zu erhalten, ist bei diesem Prüfverfahren eine präzise Probekörperfertigung von großer Bedeutung. Aufdoppler mit einer Faserorientierung von +/-45° verhindern ein unerwünschtes Versagen der Probekörper im Einspannbereich (Klemmbruch) aufgrund des Querkraftsprungs. Eine sehr sorgfältige Bearbeitung der Probekörperränder ist sicherzustellen, um komplexe Spannungssituationen und eine frühzeitige Rissinitiierung zu vermeiden. Die Verwendung von Diamantsägeblättern oder CNC-Fräsmaschinen gehört zum aktuellen Stand der Technik. Für die Durchführung der Prüfungen bei erhöhten Temperaturen sind angepasste Klebstoffe für die Aufdoppler und die Dehnungsmeßstreifen zu verwenden.
Composite Druckprüfungen
Bei der Druckprüfung von faserverstärkten Kunststoffen unterscheidet man ebenso wie bei der Zugprüfung die Prüfungen in Faserlängsrichtung (0°-Faserorientierung) und in Faserquerrichtung (90°-Faserorientierung). Für die Prüfungen sind mehrere Methoden verfügbar, die sich insbesondere in der Art der Krafteinleitung unterscheiden („Shear loading“, „End loading“ und „Combined-Loading“). Das am häufigsten verwendete Verfahren ist das „Shear-Loading“, da dieses die reale Werkstoffbelastung in einem Bauteil am ehesten nachbildet und sehr zuverlässig ist. Insbesondere beim „End-Loading“ kommt es häufig zu einem Aufplatzen der Kante des Probekörpers, da eine zu hohe Spannungskonzentration bei dieser Krafteinleitung vorliegt.
Um qualitativ hochwertige Versuchsergebnisse zu erhalten, ist bei der Druckprüfung von faserverstärkten Kunststoffen eine präzise Probekörperfertigung von großer Bedeutung. Ein Knicken der Probekörper ist nach Möglichkeit zu vermeiden, um gültige Versuchsergebnisse zu erzielen. Durch die Verwendung von zwei unabhängig voneinander messenden Dehnungsmeßstreifen wird das Knicken bestimmt. Da die Dehnungsmeßstreifen sehr klein sind und auf einer freien Probekörperlänge von nur 10 mm appliziert werden müssen, ist eine sehr präzise Ausrichtung in Längsrichtung erforderlich.
Composite Schubprüfungen
Zur Ermittlung der Schubfestigkeit sind verschiedene Verfahren etabliert. Diese unterscheiden sich in der Art der Krafteinleitung (als Druckkraft über die Probekörperkante oder als Reibungskraft über die Klemmbackensysteme) bzw. in der Geometrie der Probekörper (ungekerbt, gekerbt, miniaturisiert). Außerdem lassen sich der etablierte Zugversuch durch Faserorientierung in +/-45°-Richtung zum Schubversuch umfunktionieren sowie aus der Biegeprüfung Aussagen über die Schubfestigkeit ermitteln. Allen etablierten Verfahren ist gemein, dass sich aus ihnen nur für geringe Schubdeformationen (<5 %) und somit geringe Scherkräften belastbare Ergebnisse gewinnen lassen.
Die zuverlässige Charakterisierung von Hochleistungs-Faserverbundwerkstoffen gewinnt jedoch immer mehr an Bedeutung. Wir haben uns auf diesem Gebiet spezialisiert und bieten Ihnen neben den etablierten Prüfverfahren mit der Schubprüfung nach DIN EN ISO 20337 (vormals DIN SPEC 4885) eine von uns zusammen mit der Bundesanstalt für Materialforschung und -prüfung (BAM) maßgeblich entwickelte innovative Methode an. Mit dieser lassen sich wesentlich höhere Gleitungen und damit höhere Festigkeiten prüfen als bisher.
Composite Biegeprüfungen
Für die Biegeprüfung an faserverstärkten Kunststoffen (FVK) und an Sandwichstrukturen (Kernverbunden) werden meist die Verfahren nach DIN EN ISO 14125, DIN EN ISO 178 und DIN 53293 verwendet. Es kann eine 3-Punkt oder 4-Punkt-Belastung im Biegeversuch zum Einsatz kommen. Mittels der verschiedenen Prüfverfahren für FVK werden die Biegefestigkeit und der Biegemodul unter einer Biegebeanspruchung der Probe bei definierten Prüfbedingungen ermittelt. Das Prinzip der Biegeprüfung besteht in einer zweiteiligen Biegevorrichtung, in der der Probekörper als Biegebalken zwischen zwei äußeren Auflagern eingespannt und über ein (3-Punkt) oder zwei (4-Punkt) innere Auflager belastet wird. Die Prüfung erfolgt bei konstanter Geschwindigkeit bis zu einer vorgegebenen Verformung oder bis zum Versagen der Probe. Als Ergebnis werden die Biegespannung und der Biegemodul ermittelt.
Bei der Beanspruchung von Composite- oder Sandwich-Material auf 4-Punkt-Biegung stellt sich zwischen den inneren Auflagern ein über die Probekörperlänge konstanter Dehnungs- und Biegeverlauf ein, was ein Vorteil gegenüber dem 3-Punkt-Biegeversuch darstellt. Es ist zu beachten, dass beim 4-Punkt- Biegeversuch zwischen den äußeren und den inneren Auflagern eine zusätzliche Schubbeanspruchung auftritt. Die Auflagerabstände, d.h. die Hebelarme sind so zu wählen, dass die Schubfestigkeit des Werkstoffs unterschritten wird. Der Prüfbereich zwischen den inneren Auflagern ist frei von Schubspannungen.
Composite ILSS-Prüfungen
Das Kurzbiegeprüfverfahren zur Bestimmung der scheinbaren interlaminaren Scherfestigkeit (ILSS) ist eine Modifizierung der 3-Punkt-Biegeprüfung. Der Auflagerabstand ist im Verhältnis zur Probekörperdicke gering, wodurch der Probekörper auf Scherung belastet wird. Der Probekörper ist ein kurzer Balken aus einer thermo- oder duroplastischen Matrix mit einer Faserverstärkung in 0°- bzw. 0°/90°-Richtung. Mit scheinbarer interlaminarer Scherfestigkeit bezeichnet die Norm „die in der halben Dicke des Probekörpers vorliegende maximale Scherspannung im Augenblick des ersten Versagens“.
Die Norm weist auf Einschränkungen dieser Prüfmethode hin. Je nach Werkstoffauswahl kann „das Ergebnis durch verschiedene Kopplungen wie Dehnung/Biegung und Biegung/Verdrehung usw. beeinflusst werden.“ Es ist möglich, daß der Probekörper aufgrund von Biegung oder plastischer Verformung versagt. Eine Aussage zur tatsächlichen Scherspannung im Augenblick des Versagens ist dann nicht möglich. Zur Festlegung konstruktiver Größen ist das Verfahren ungeeignet. Es kann jedoch zur Werkstoffvorauswahl oder zur Qualitätskontrolle eingesetzt werden. Der ermittelte Wert ist kein absoluter Wert, Prüfergebnisse sind nur innerhalb einer Serie vergleichbar. Den Nachteilen steht als Vorteil gegenüber, daß das ILSS-Verfahren sehr kleine und geometrisch einfache Probekörper benötigt. Mit wenig Materialaufwand wird eine qualitative Aussage zur Faser-Matrix-Bindung erzeugt.
Composite Sandwich-Prüfungen
Verbundwerkstoffe, die aus Decklagen und einem Kernmaterial aufgebaut sind, werden als Sandwich-Strukturen bezeichnet. Die äußeren Decklagen bestehen dabei aus zwei dünnen, aber steifen Laminaten, die in der Regel in 0°- bzw. 0°/90°-Faserorientierung aufgebaut sind. Das Kernmaterial ist im Vergleich dazu erheblich dicker und weist eine signifikant geringere Festigkeit auf. Durch die Verlagerung der äußeren Decklagen weg von der neutralen Faser erhalten Sandwich-Strukturen ihre bei einer insgesamt geringen Dichte hohe Biegefestigkeit (Ausnutzen des Steiner-Anteils).
Für die Kernmaterialien werden üblicherweise offen- oder geschlossenporige Schaumstoffe, z.B. aus Polyurethan, Polyethylen oder Polystyrol, verwendet. Auch Balsaholz oder Wabenstrukturen aus Kunststoff, Papier oder Aluminium kommen zum Einsatz. Die Decklagen bestehen in der Regel aus glas- oder kohlenstofffaserverstärkten Kunststoffen mit duroplastischer oder thermoplastischer Matrix. Die Verklebung des Kernmaterials mit den Decklagen ist anspruchsvoll und stellt aufgrund der Biegebelastung der Struktur (interlaminare Schubbeanspruchung im Verbund) besondere Anforderungen an den Verarbeiter.
Composite Klebeprüfungen
Als Fügeverfahren für Bauteile aus faserverstärkten Kunststoffen und Composites kommen in der Regel Verklebungen zum Einsatz. Diese verbinden die einzelnen Komponenten der Bauteile miteinander und müssen denselben Belastungen wie die einzelnen Strukturelemente aus FKV selbst standhalten. Die Klebstoffe basieren häufig auf thixotropierten Duromerwerkstoffen (Epoxidharz- oder Vinylesterharzsysteme), jedoch kommen auch dauerelastische Verklebungen (Kunstkautschuke) zum Einsatz. Weitere Basiswerkstoffe sind Polyurethane bzw. Cyanate, Silikone und Acrylate. Neben der reinen mechanischen Belastung der Klebstoffsysteme spielen für die Auswahl vor allem äußere Einflüsse wie UV-Strahlung, ausgesetzte Medien und Temperaturen eine entscheidende Rolle.
Entscheidend für eine ordnungsgemäße Verklebung ist die physikalische, chemische und mechanische Bindung (Kohäsion und Adhäsion). Diese kann nur dann erreicht werden, wenn die einzelnen Arbeitsschritte des Verklebens entsprechend den allgemeinen Verfahrensanweisungen und nach den Vorgaben des Klebstoffherstellers eingehalten werden. Die Beanspruchungsarten von Klebeverbindungen lassen sich in Zug-, Spalt-, Zugscher- und Schälbeanspruchung gliedern. Weitere Informationen sind u.a. in DIN 53281-1…3, DIN 53283, DIN 54451 und VDI 2229 aufgeführt.
Composite Betriebsfestigkeit
Das Ermüdungsverhalten von faserverstärkten Kunststoffen ist für die Lebensdauervorhersage von Bauteilen und Strukturen von großer Bedeutung. Das Verhalten dieser Werkstoffe unter zyklischer Belastung unterscheidet sich dabei stark vom Verhalten isotroper Materialien wie beispielsweise metallische Werkstoffe. Bei Faser-Kunststoff-Verbunden erfolgt die Ermüdung im wesentlichen durch die Entstehung, das Wachstum und die Ausbreitung einer Vielzahl von Einzelrissen. Die Schädigungsentwicklung ist dabei signifikant vom Aufbau des Laminats, der Matrix und von den verwendeten Fasern abhängig. Der Schädigungsablauf ist materialspezifisch, erfolgt aber typischerweise in folgenden Phasen:
- Entstehung von Querrissen in Laminatschichten außerhalb der Belastungsrichtung
- Entstehung von Längsrissen entlang lasttragender Fasern
- Delaminationen entlang von Probekörperkanten
- Delaminationen im Inneren der Probekörper aufgrund von Quer- und Längsrissen
- Bruch lasttragender Fasern aufgrund des Ausknickens von Fasern
- Faser-Matrix-Ablösungen aufgrund von Schubbeanspruchungen
- Komplettes Versagen der Probe / des Bauteils
Bei Grasse Zur Composite Testing werden Faser-Kunststoff-Verbunde unter Zug-Druck-Wechsellast (Lastverhältnis R = -1), Zug-Zug-Schwelllast (Lastverhältnis R = 0,1) oder Druck-Druck-Schwelllast (Lastverhältnis R = 10) geprüft. Dabei wird die Belastungsart über die Faserorientierung definiert. Eine Faserorientierung in 0°-, 90°- oder 0°/90°-Richtung führt zu Zug- bzw. Druckbelastungen, eine Faserorientierung in +/-45°-Richtung führt zu Schubbelastungen. Zur Vermeidung vorzeitigen Faserausknickens wird eine Knickstütze (z.B. GZ BS-32) verwendet werden.
Mit einer für die zyklische Prüfung geeigneten 3-Punkt- / 4-Punkt-Wechselbiegevorrichtung (z.B. GZ B-50) werden die Biegeeigenschaften (interlaminarer Schub) von faserverstärkten Kunststoffen und Sandwich-Materialien charakterisiert. Über eine Variation der Faserorientierung können zusätzliche Aussagen zu den Zug- und Druckeigenschaften der Materialien gewonnen werden. Das Ermüdungsverhalten wird dabei an verschiedenen Werkstoffen wie beispielsweise lang- oder endlosfaserverstärkte Kunststoffe mit duro- oder thermoplastischer Matrix untersucht. Zur Auswertung werden qualitative Aussagen, Wöhlerlinien, Basquin-Geradengleichungen oder Haigh-Diagramme erzeugt. Bei der Interpretation der Daten kann auf ein langjähriges Know-how zurückgegriffen werden.
Composite Thermische Analyse
Die thermoanalytische Untersuchung von faserverstärkten Kunststoffen spielt für die Charakterisierung der Materialeigenschaften eine große Rolle. Insbesondere für die Bestimmung von matrixdominanten Materialeigenschaften (Zwischenfaserbruch) wie Schub- oder Querzugkennwerte ergibt sich nur durch die Kenntnis der Matrixeigenschaften ein vollständiges Bild. Liegt beispielsweise eine unvollständige Härtung vor (Alpha < 95 %), stehen sogenannte Härtungsreserven zur Verfügung, die die Druckfestigkeit insbesondere bei erhöhten Temperaturen signifikant erhöhen können.
Auch ist eine Bestimmung der aktuellen und der maximalen Glasübergangstemperatur Tg sinnvoll, um z.B. den Einfluss der Temperung und des Mischungsverhältnisses bestimmen zu können. Dabei stehen verschiedene Verfahren wie DSC oder DMA zur Verfügung, die auf unterschiedliche physikalische Weise die Informationen liefern.
Anfrage Formular
Bitte füllen Sie für die Zusendung eines Angebotes das nachfolgende Formular aus. Sollte die gewünschte Prüfnorm nicht aufgeführt sein, geben Sie die Norm bitte im Kommentarfeld ein. Bei größeren Prüfumfängen verwenden Sie bitte ebenfalls das Kommentarfeld. Nach Versand der Prüfanfrage erhalten Sie von uns zeitnah ein unverbindliches Angebot.
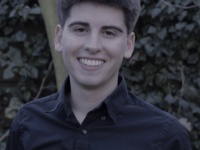
Ihr Ansprechpartner
Tarik Randelhoff, M.Sc.
Leiter des akkreditierten Materialprüflabors
+49 30 7790791-60
tarik.randelhoff@grassezur.de