Composite Testing Services
Test laboratory accredited according to DIN EN ISO/IEC 17025:2018
Overview
At its Berlin site, Grasse Zur Composite Testing offers a wide range of material testing according to all common test methods for fiber-reinforced plastics. The testing services are carried out in the DIN EN ISO 17025:2018 accredited laboratory and cover the entire spectrum of material testing. The clients often come from development departments (simulation or new development) or production (incoming goods or production-accompanying quality assurance) in the aerospace, automotive or chemical industries. The focus of the testing services lies equally in the quasi-static (and sometimes strain rate-development) material testing, the cyclical material testing (fatigue tests) and thermal analysis (DSC, DMA, etc.). The tests are carried out in accordance with all common test procedures according to DIN EN ISO or ASTM. Additionally, the employees of Grasse Zur have extensive know-how from many other technical fields.
To determine the quasi-static material properties, tests are carried out on electromechanical testing machines in the force range of 1 to 100 kN. The cyclical material tests are implemented using a servo hydraulic testing machines in the force of 1 to 50 kN. The clamp is tested with flat and round hydraulic cable clamping systems (1 to 25 mm). One-stage and multi-stage fatigue tests on the servohydraulic testing machines can determine Wöhler lines and Haigh diagrams. Extensive test equipment is available for a wide variety of test requirements.
Portfolio
The range of services offered covers the complete field of material testing, from the production of laminates in the VARI process via CNC-controlled test to the execution of material testing. Optional tests include the degree of cure or fiber volume content and the conditioning of specimens and tests at different temperatures. Special test requirements, such as storage in fuels or fractographic examinations of micrographs, are implemented quickly and flexibly. The production and testing of pure resin materials from EP or VE resin systems is offered as well as drop tests for evaluation of splinter protection. Only calibrated measuring equipment is used for the tests. In accordance with aerospace requirements, only strain gauges and Poisson numbers are used to determine the moduli and to ensure accurate measurement of material deformation.
-
Order Confirmation
After quoting and commissioning, the client receives an order confirmation
-
Material Input
The material input is documented according to our accreditation ISO 17025
-
Schedule
On the day the material is received, the client will be given a detailed testing timeline
-
Test Specimen Production
Production takes place with CNC-controlled machines and possibly also includes DMS application
-
Measurement
The finished test specimens are measured with calibrated measuring equipment
-
Testing
The material testing is carried out on universal testing machines or analyzers
-
Preparation of Test Reports
The test reports contain a clear overview of the results and detailed photos
-
Dispatch of the Tested Specimens
Depending on the order, the shipment of the tested samples is securely packed
-
Summary
At the end of the test project, the client receives a clear summary of the results
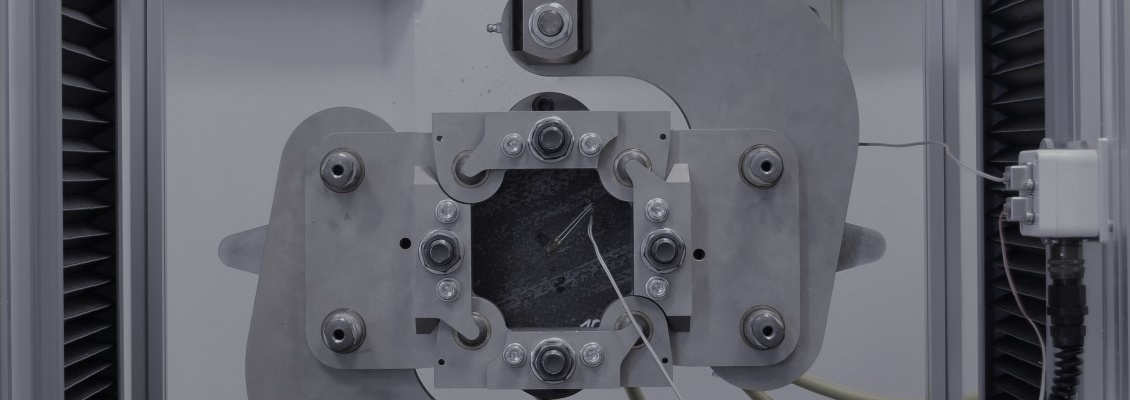
Composite Tensile Tests
In the tensile test, the mechanical material properties are determined under quasi-static tensile loading. The tensile test is one of the most commonly used test methods and is also used for composite materials such as carbon and glass fiber reinforced plastic. Basically, a distinction is made between isotropic, anisotropic and orthotropic materials. In the case of anisotropic materials, a fiber breakage load (FB) results in the fiber longitudinal direction (0° fiber orientation) and an intermediate fiber breakage load (IFB) in the fiber transverse direction (90° fiber orientation).
In order to obtain high-quality test results, a precise specimen production is of great importance in this tensile tests. Doppler with a fiber orientation of +/- 45 ° prevents unwanted failure of the specimens in the clamping area (clamping break) due to the lateral force jump. Ensuring very careful processing of the specimen edges is essential in order to avoid complex stress situations and early crack initiation. The use of diamond saw blades or CNC milling machines is state of the art. For carrying out the tests at elevated temperatures, suitable adhesives for the doublers and the strain gauges are used.
Composite Compressive Tests
In the pressure testing of fiber-reinforced plastics, as in the tensile test, a distinction is made between tests in the fiber longitudinal direction (0° fiber orientation) and in the fiber transverse direction (90° fiber orientation). Several methods are available for the tests, which differ in particular in the type of force application (“shear loading”, “end loading” and “combined loading”). The most commonly used method is shear loading, as this most closely simulates the real material load in a component and is very reliable. In the case of end loading, the edge of the test specimen often bursts, since there is an excessively high concentration of stress during this introduction of force.
In order to obtain high quality test results, accurate specimen production is of great importance in the pressure testing of fiber reinforced plastics. Buckling of specimens should be avoided in order to obtain valid test results. By using two independently measuring strain gauges, buckling is determined. Since the strain gauges are very small and must be applied to a free specimen length of only 10 mm, a very precise alignment in the longitudinal direction is required.
Composite Shear Tests
Various test methods are established for determining the shear strength. These differ in the type of load application (as a compressive load via the specimen edge or as a frictional load via the clamping jaw systems) or in the geometry of the specimens (unnotched, notched, miniaturised). In addition, the widely used tensile test can be converted into a shear test through fibre orientation in the +/-45° direction and statements about the shear strength can be determined from the bending test. All established methods have in common that they can only be used to obtain reliable results for low shear deformations (< 5 %) and thus only for low shear loads.
However, the reliable characterisation of high-performance fibre composites is becoming increasingly important. We have specialised in this field and, in addition to the established test methods, we offer you the shear test according to DIN EN ISO 20337 (formerly DIN SPEC 4885), an innovative test method that we developed together with the Federal Institute for Materials Research and Testing. With this test method, significantly higher shear loads and thus higher strengths can be tested than before.
Composite Bending Tests
The procedures according to DIN EN ISO 14125, DIN EN ISO 178 and DIN 53293 are mostly used for the bending tests on fiber reinforced plastics (FRP) and on sandwich structures (core composites). A 3-point or 4-point load can be used for the bending test. By means of the various test methods for FRP, the bending strength and the flexural modulus are determined under a bending load of the specimen under defined test conditions. The principle of the bending test consists in a two-part bending process, in which the specimen is clamped as a bending beam between two outer supports and loaded via one (3-point) or two (4-point) inner supports. The test is carried out at a constant increasing speed to a given deformation or until the failure of the sample. As a result, the bending stress and the flexural modulus are determined.
When stressing composite or sandwich material, a 4-point bend has an advantage over the 3-point bending test. A 4-point bend has a constant expansion and a bending curve occurs between the inner supports. It should be noted that in the 4-point bending test between the outer and inner supports an additional shear stress occurs. The bearing distances, i.e. the lever arms, are to be selected so that the shear strength of the material is undercut. The test area between the inner supports is free of shear stress.
Composite ILSS Tests
The Short Bend Test Method for Determining Apparent Interlaminar Shear Strength (ILSS) is a modification of the 3-point bend test. The bearing distance is small in relation to the specimen thickness, whereby the specimen is subjected to shear stress. The specimen is a short bar made of a thermosetting or thermosetting matrix with a fiber reinforcement in the 0 ° or 0 ° / 90 ° direction. With apparent interlaminar shear strength, the standard refers to “the maximum shear stress in half the thickness of the specimen at the moment of the first failure”.
The standard indicates limitations of this test method. Depending on the material selection, “the result may be influenced by various couplings such as elongation/bending/twisting etc”. It is possible that the specimen will fail due to bending or plastic deformation. A statement about the actual shear stress at the moment of failure is then not possible. To determine constructive sizes, the method is unsuitable. However, it can be used for material preselection or for quality control. The calculated value is not an absolute value, test results are comparable only within a series. The disadvantage is that the ILSS method requires very small and geometrically simple specimens. With little material expenditure, a qualitative statement about the fiber-matrix bond is generated.
Composite Sandwich Tests
Composite materials that consist of cover layers and a core material are called sandwich structures. The outer cover layers consist of two thin but stiff laminates, which are usually built up in 0° or 0°/90° fibre orientation. The core material is considerably thicker in comparison and has a significantly lower strength. By shifting the outer cover layers away from the neutral fibre, sandwich structures obtain their high flexural strength with an overall low density (exploiting the Steiner component).
Open- or closed-cell foams, e.g. made of polyurethane, polyethylene or polystyrene, are usually used for the core materials. Balsa wood or honeycomb structures made of plastic, paper or aluminium are also used. The cover layers are usually made of glass or carbon fibre reinforced plastics with thermosetting or thermoplastic matrix. The bonding of the core material with the cover layers is demanding and places special requirements on the processor due to the bending load of the structure (interlaminar shear stress in the composite).
Composite Adhesive Tests
As a rule, bonding is used as a joining method for components made of fibre-reinforced plastics and composites. These join the individual components of the parts together and must withstand the same loads as the individual structural elements made of FRP themselves. The adhesives are often based on thixotropic duromer materials (epoxy resin or vinyl ester resin systems), but permanently elastic bonds (synthetic rubbers) are also used. Other base materials are polyurethanes or cyanates, silicones and acrylates. In addition to the purely mechanical load of the adhesive systems, external influences such as UV radiation, exposed media and temperatures play a decisive role in the selection.
Decisive for proper bonding is the physical, chemical and mechanical bond (cohesion and adhesion). This can only be achieved if the individual steps of the bonding process are followed according to the general procedural instructions and in accordance with the adhesive manufacturer’s specifications. The types of stress on bonded joints can be divided into tensile stress, split stress, tensile shear stress and peel stress. Further information can be found in DIN 53281-1…3, DIN 53283, DIN 54451 and VDI 2229, among others.
Composite Service Strength
Measuring the fatigue behaviour of fibre-reinforced plastics is the key to predict service lifetime of parts and structures, whereat the anisotropic materials show a very different behaviour from isotropic materials like metals. For composites, fatigue is essentially created by initiation, growth and propagation of a multitude of cracks. The evolution of damage is influenced not only by the materials of matrix and fibres but also by the composition of the laminate. Although it is highly specific to the individual material, it usually follows the stages below:
- Initiation of lateral cracks in laminate layers out of loading direction
- Initiation of longitudinal cracks alongside load-bearing fibres
- Delaminationen alongside rim of specimen
- Internal delamination due to lateral and longitudinal cracks
- Fracture of load-bearing fibres due to buckling
- Delamination due to shear stress
- Complete failure of the part or specimen
At Grasse Zur Composite Testing, fibre-reinforced plastics are tested under tensile-compressive alternating load (load ratio R = -1), tensile-tensile load (load ratio R = 0.1) or compressive-compressive load (load ratio R = 10). The load type is defined by the fibre orientation. A fibre orientation in 0°, 90° or 0°/90° direction leads to tensile or compressive loads, a fibre orientation in +/-45° direction leads to shear loads. To avoid premature fibre buckling, a buckling support (e.g. GZ BS-32) will be used.
The bending properties (interlaminar shear) of fibre-reinforced plastics and sandwich materials are characterised with a 3-point / 4-point alternating flexure fixture (e.g. GZ B-50) suitable for cyclic testing. By varying the fibre orientation, additional information on the tensile and compressive properties of the materials can be obtained. The fatigue behaviour is investigated on different materials such as long or continuous fibre-reinforced plastics with thermoset or thermoplastic matrix. Qualitative statements, S/N curves, Basquin line equations or Haigh diagrams are generated for evaluation. When interpreting the data, it is always possible to fall back on many years of know-how.
Composite Thermal Analysis
The thermoanalytical test of fiber reinforced plastics plays a large role in the characterization of material properties. In particular to the determination of the matrix dominating material qualities (intermediate fiber fracture) like shear or transverse tensile properties, a complete picture results only through the knowledge of matrix properties. For example, if there is an incomplete cure (Alpha <95%), cure reserves are available, which can significantly increase the compressive strength, especially at elevated temperatures.
Also, a determination of the actual and maximum glass transition temperatures Tg is useful, e.g. to be able to determine the influence of tempering and the mixing ratio. There are several methods available, such as DSC or DMA, which provide the information in different physical ways.
Composite Standard Overview
Fibre-reinforced plastics can be tested according to a variety of national and international standards. These standards differentiate according to the material of the fibre or the matrix, the fibre orientation or other criteria. In addition, there are a large number of manufacturer’s or factory standards which partly supplement the national and international standards or differ in individual points.
In the following, a series of standards are listed which are usually used for the testing of fibre-reinforced plastics. The list is divided into the typical tests such as tensile tests or shear tests. If you have any questions about the individual standards or would like to receive a quotation for a standard that is not listed, we would be pleased to receive your enquiry.
Request Form
Please fill out the following form to receive a quotation. If the desired test standard is not listed, please enter the standard in the comment field. For larger test scopes, please also use the comment field. After sending the test request, you will receive a non-binding offer from us in a timely manner.
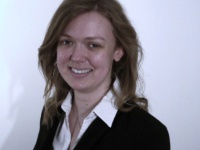
Your contact person
M.Sc. Nadine von der Eltz
Head of test laboratory
+49 30 7790791-61
nadine.vondereltz@grassezur.de